Southern
Pacific
1218
Starting The Engine And Replacing A Leaky Liner
When the 1218 arrived on the
property, there was no cooling water in the block. We checked
the
crankcase for water and were pleased to see that there was
none.
It is not uncommon for locomotive diesel engines, especially 50 year
old ones, to have internal water leaks so no
water in the oil was a good sign. We pulled all the injectors
and
put about a half cup of Marvel Mystery Oil in each cylinder to insure
that there was lubrication in the bores. After some other
preliminary work, we filled the block with water, jumped the
batteries on the 1218 to another locomotive and began
cranking
the engine. It took quite a bit of time to get it to fire but
when it did, there was a very satisfying eruption of black smoke from
the stack and it settled down to run quite nicely. The smoke
is
caused by the lag in the turbocharger coming up to speed and
supplying engine with the combustion air it needs.
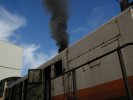 |
A few days after the successful
engine start, I was
working on something and noticed that there was oil dripping from under
the engine. Investigation revealed that oil was running out
of
the dip stick hole due to water in the oil pan which had raised the oil
level higher than it should be. And so began a journey
through
the reasons why a 6-251 Alco engine would have water in the oil
pan. Ultimately, we discovered that the number 5
cylinder liner was the culprit. Unlike most gasoline engines,
many diesel engines have replaceable cylinders, called
"liners".
I placed an order with Hatch
& Kirk in Seattle for a liner, piston rings, connecting rod
bearings and the necessary gaskets. We had to make a set of
special tools that are required to pull the liner and the piston and
then install the new liner. We did not get any photos of the
first part of the process but the effort resulted in the cylinder head,
piston and connecting rod sitting on a pallet.
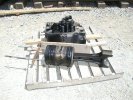 |
The liner is pushed into
its hole in the block by hydraulic pressure so it is necessary to apply
a lot of pull to get it out. The bar across the top of the
liner
supports a 1" threaded rod which is attached to a bar across the bottom
of the liner. Turning the nut on the top of the rod results
in
pulling the bar and the liner up. Once the liner pops loose
from
its sealing surfaces, it easily lifts out.
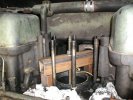 |
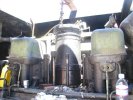 |
Once the liner was out,
it was easy
to see the defect that caused the water leak. The problem is
called "cavitation". When combustion takes place in the
cylinder,
pressure waves are created within the water surrounding the
cylinder. If the reader is interested in the effects of
cavitation in an engine, the internet has thousands of technical
treatises on the subject. Suffice it to say that it is a bad
thing and caused the void seen in the side of the liner in the photo
#1. Photo #2 shows the surface of the block directly
opposite the liner damage. Luckily, these holes are not in a
critical area.
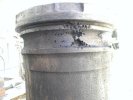 |
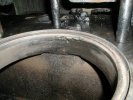 |
In keeping with standard
Alco
practice, there is no head gasket used in the 6-251 engine.
The
mating surfaces of the head and liner are ground using fine grinding
compound and a special surfacing tool. Lacking that tool, we
inverted the head and set the liner in place on the head.
With a
coating of fine valve grinding compound in place between the had and
liner, Jon and Rich proceeded to turn the liner against the head and
let gravity do the grinding work. After a few minutes of
this,
the liner would be removed, both surfaces cleaned, and the process
started again until there was a good mating surface all the way around.
The
process of
installing liner involves using a large hydraulic jack to push the
liner in place. The jack seen is attached to a hand operated
hydraulic pump. The jack is sitting on a 1" steel plate which
is
in turn sitting on the top liner surface. The water sealing
"O"
rings on the liner were lubricated with Vasoline before the liner was
jacked into place.
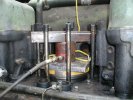 |
In order to put
the piston in the liner, it is necessary to compress the sealing rings
on the piston, Our machinist Dan Espinosa made a ring
compressor
out of the old liner. After machining the liner for the new
purpose, it is easy to see the cavitation damage. The
compressor
was put in place and the piston dropped down through the compressor and
into the liner. A little pressure was necessary to get the
piston
to drop and care must be taken to have the rod bearing go over the
crankshaft properly. Rich is seen operating a small ratchet
lift
attached to the piston. After this, the lower rod cap was put
in
place and the rod cap bolts properly tightened. Now, we have
only
5 more potential leakers. (This turned out to be a very prophetic statement)
|